Effective Inventory Management Strategies to Optimize Costs
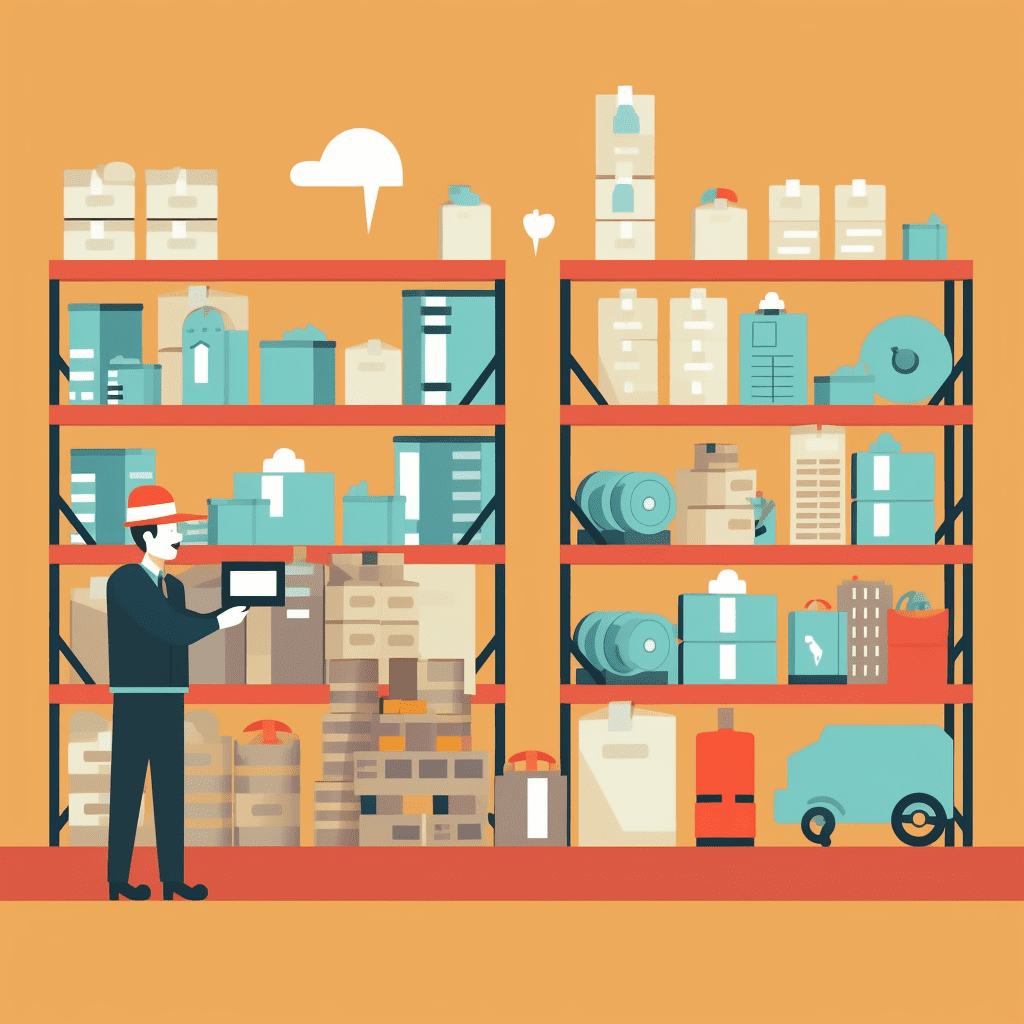
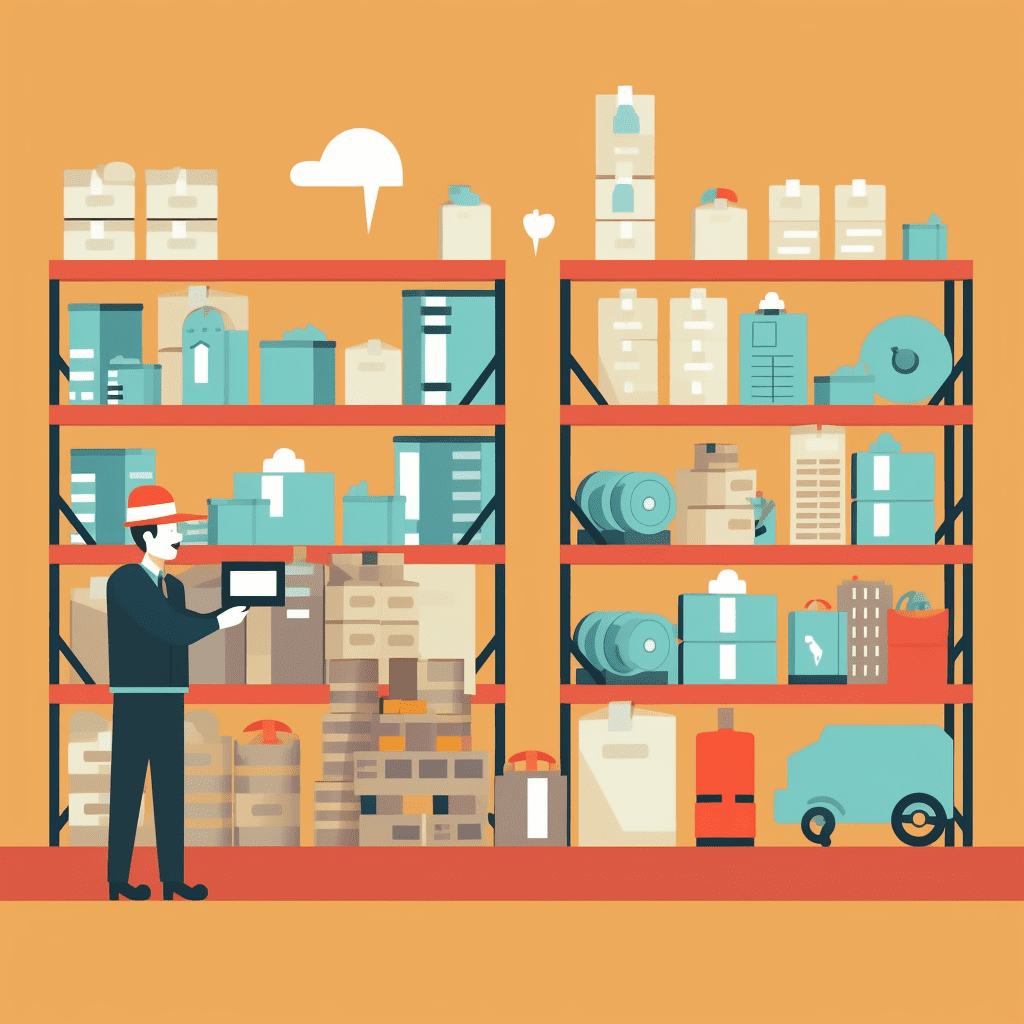
Inventory management plays a crucial role in the success of any business, regardless of its size or industry. Effectively managing inventory can significantly impact a company’s bottom line, as it directly affects costs, cash flow, and customer satisfaction. In this article, we will explore essential inventory management strategies that businesses can implement to optimize costs and achieve efficiency.
Understanding Inventory Management
2.1 What is Inventory Management?
Inventory management refers to the process of overseeing and controlling a company’s stocked goods. It involves balancing the costs associated with holding inventory against the benefits of having products readily available for customers. Proper inventory management ensures that a business can meet customer demand without excessive stockpiling or stockouts.
2.2 Importance of Effective Inventory Management
Effective inventory management is vital for several reasons. It helps prevent overstocking, which ties up capital and leads to increased holding costs. On the other hand, understocking can result in missed sales opportunities and dissatisfied customers. By striking the right balance, businesses can minimize costs and maximize profits.
Key Strategies for Efficient Inventory Management
3.1 ABC Analysis
The ABC analysis categorizes inventory items into three groups based on their value and importance. Class A items are high-value products that contribute significantly to revenue but represent a smaller portion of the inventory. Class B items are moderately important, while Class C items are low-value but may have a high consumption rate. Prioritizing inventory management based on ABC analysis helps focus efforts where they are most needed.
3.2 Just-In-Time (JIT) Inventory System
JIT is a lean inventory management approach where products are ordered and received only when needed for production or customer demand. By reducing excess inventory, JIT minimizes holding costs and eliminates the risk of obsolete items. However, its success relies on efficient supplier relationships and accurate demand forecasting.
3.3 Economic Order Quantity (EOQ) Model
The EOQ model determines the optimal order quantity that minimizes total inventory costs, including holding and ordering costs. Striking the right balance helps businesses avoid over-ordering, which can lead to excess stock, or under-ordering, which causes stockouts and missed sales.
3.4 Vendor-Managed Inventory (VMI)
VMI is a collaborative approach where suppliers monitor and manage a customer’s inventory levels. Suppliers take responsibility for replenishing stock based on data shared by the customer. This strategy reduces the burden on the customer while ensuring a continuous supply of goods.
3.5 Demand Forecasting and Inventory Planning
Accurate demand forecasting is critical for effective inventory management. By analyzing historical data and market trends, businesses can anticipate customer demand and plan inventory levels accordingly. This minimizes the risk of stockouts and excess inventory.
Technology’s Role in Inventory Management
4.1 Inventory Management Software
Inventory management software provides businesses with the tools to efficiently track and manage their inventory. It automates tasks such as order processing, stock tracking, and reporting, streamlining the entire inventory management process.
4.2 Internet of Things (IoT) in Inventory Management
The IoT enables real-time tracking of inventory through interconnected devices. RFID tags and sensors can monitor inventory levels, location, and condition, providing valuable data for better decision-making.
4.3 RFID Technology for Inventory Tracking
RFID technology uses radio-frequency signals to track inventory items throughout the supply chain. It offers increased accuracy and speed compared to manual tracking methods.
Reducing Costs through Inventory Optimization
5.1 Minimizing Holding Costs
Holding costs include expenses like storage, insurance, and depreciation. Businesses can reduce these costs by optimizing warehouse space, using efficient storage systems, and implementing proper inventory rotation techniques.
5.2 Reducing Ordering Costs
Ordering costs encompass expenses related to placing and receiving orders, such as order processing and transportation. By consolidating orders and negotiating favorable terms with suppliers, businesses can lower their ordering costs.
5.3 Managing Lead Times
Lead times refer to the time it takes for an order to be delivered after it’s placed. By analyzing lead times and working closely with suppliers, businesses can ensure a steady flow of inventory and minimize the risk of stockouts.
Streamlining Inventory Control and Monitoring
6.1 Cycle Counting and Regular Audits
Cycle counting involves regularly counting a portion of inventory to identify discrepancies and inaccuracies. Regular audits help maintain accurate inventory records and prevent theft or inventory shrinkage.
6.2 Safety Stock Management
Safety stock acts as a buffer to protect against unexpected fluctuations in demand or supply chain disruptions. Carefully managing safety stock levels ensures a business can handle unforeseen situations without incurring excessive costs.
6.3 FIFO and LIFO Inventory Methods
The First-In-First-Out (FIFO) and Last-In-First-Out (LIFO) methods determine how inventory is issued. FIFO is suitable for perishable goods, while LIFO may be beneficial for businesses aiming to offset tax liabilities. Choosing the right method can impact costs and financial reporting.
Emphasizing Supplier Relationships
7.1 Establishing Strong Partnerships
Building strong relationships with suppliers fosters collaboration and communication, leading to more favorable terms and reliable supply chains.
7.2 Negotiating Favorable Terms
Skillful negotiation can result in discounts, extended payment terms, and improved overall pricing. This helps businesses lower their procurement costs and increase profit margins.
The Impact of Forecasting Accuracy on Inventory Management
8.1 Collaborative Planning, Forecasting, and Replenishment (CPFR)
CPFR involves collaboration between suppliers and customers to develop accurate forecasts and efficient inventory replenishment plans. By sharing data and insights, businesses can optimize inventory levels and avoid stockouts.
8.2 Real-time Data Analysis
Using real-time data analytics helps businesses respond quickly to changes in demand or supply, making inventory management more agile and cost-effective.
Handling Seasonal Demands and Fluctuations
9.1 Seasonal Inventory Management Strategies
For businesses dealing with seasonal fluctuations, planning and adjusting inventory levels accordingly are crucial. This ensures optimal stock during peak demand periods and avoids excess inventory during slow seasons.
9.2 Inventory Pooling and Centralized Warehousing
Pooling inventory from multiple locations or centralizing warehousing can lead to cost savings and improved efficiency, especially for businesses with a widespread customer base.
Sustainable Inventory Practices
10.1 Green Inventory Management
Adopting eco-friendly practices in inventory management not only benefits the environment but can also reduce costs through resource conservation.
10.2 Reverse Logistics and Recycling
Implementing a robust reverse logistics system allows businesses to recover value from returned products or recycle materials, contributing to cost optimization and sustainability.
Case Studies: Successful Inventory Management Implementations
11.1 Company A: Improving Efficiency with JIT
Company A implemented a Just-In-Time inventory system, reducing excess inventory levels and eliminating holding costs. This improved cash flow and overall efficiency.
11.2 Company B: Streamlining Inventory with VMI
Company B collaborated with its suppliers through Vendor-Managed Inventory, resulting in improved inventory control and better demand forecasting.
Challenges in Inventory Management
12.1 Balancing Costs and Customer Satisfaction
Finding the right balance between inventory costs and meeting customer demand can be challenging. Businesses must continually analyze data and adjust strategies to maintain efficiency.
12.2 Inventory Forecasting Errors
Forecasting errors can lead to either overstocking or stockouts, impacting costs and customer satisfaction. Regularly reviewing and improving forecasting methods can mitigate these issues.
12.3 Inventory Theft and Loss Prevention
Businesses need to implement security measures to prevent inventory theft, as losses can significantly impact costs and profitability.
Conclusion
Effective inventory management is essential for businesses aiming to optimize costs while meeting customer demands. By implementing strategies such as ABC analysis, JIT, and VMI, and leveraging technology for tracking and forecasting, companies can achieve efficient inventory management and cost optimization. Sustainable practices, strong supplier relationships, and a focus on accurate forecasting further contribute to successful inventory management. By addressing challenges proactively, businesses can maintain a competitive edge and ensure long-term success.
FAQs
- What are the main benefits of effective inventory management? Effective inventory management leads to optimized costs, reduced holding and ordering expenses, improved customer satisfaction, and increased profitability.
- What is the significance of demand forecasting in inventory management? Demand forecasting helps businesses plan their inventory levels accurately, ensuring they have the right amount of stock to meet customer demand without overstocking.
- How can technology aid in inventory management? Inventory management software, IoT, and RFID technology provide real-time tracking, data analysis, and automation, streamlining the inventory management process.
- What is the impact of seasonal inventory management strategies on businesses? Seasonal inventory management allows businesses to align inventory levels with fluctuating demand, preventing excess stock during slow seasons and shortages during peak periods.
- How can businesses handle challenges in inventory management effectively? Businesses can address challenges by continually analyzing data, improving forecasting accuracy, implementing robust security measures, and fostering collaborative supplier relationships.
Sources: Proventainternational.com
Co-Author: J.P.A
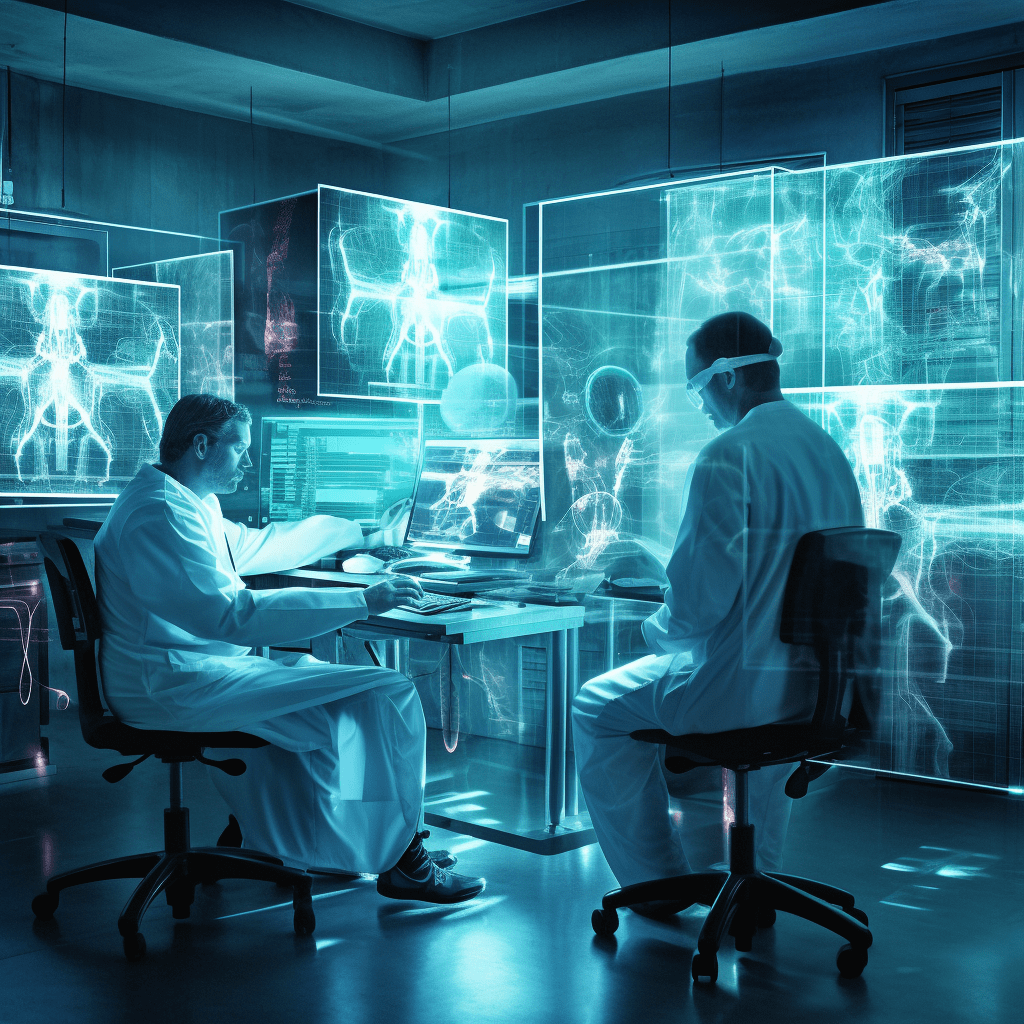
Navigating the Complex World of Global Regulatory Affairs in Oncology
In today's fast-paced global pharmaceutical landscape, the regulatory affairs sector plays a pivotal role in ensuring the safety, efficacy, and market access of oncology drugs. As the demand for innovative cancer therapies continues to grow, understanding the intricacies of global...
2 years agoNavigating the Complex World of Global Regulatory Affairs in Oncology
In today's fast-paced global pharmaceutical landscape, the regulatory affairs sector plays a pivotal role in ensuring the safety, efficacy, and market access of oncology drugs. As the demand for innovative cancer therapies continues to grow, understanding the intricacies of global...
2 years ago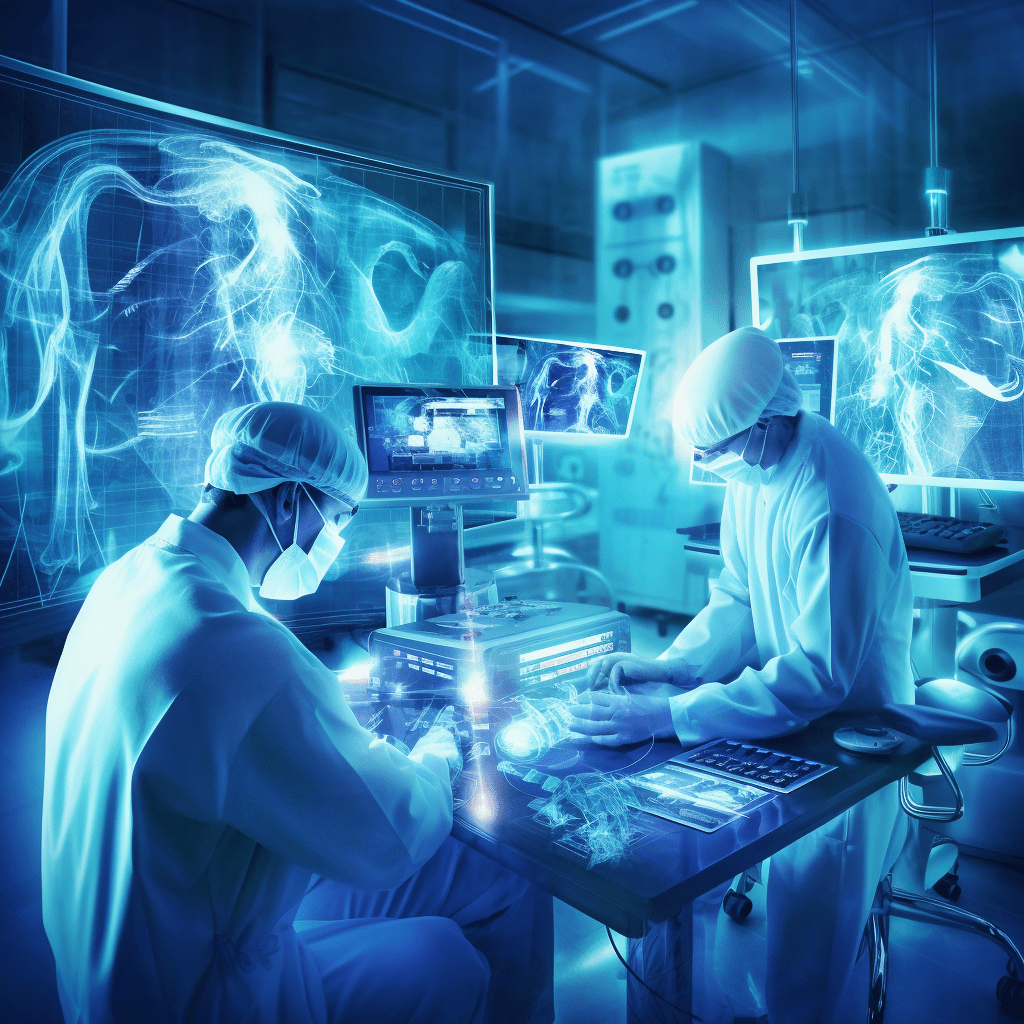
Overcoming the Hurdles: Navigating the Challenges in Oncology Clinical Trials
In the world of medical research, oncology clinical trials are at the forefront of innovation and discovery. These trials play a crucial role in advancing our understanding of cancer and developing more effective treatments. However, the path to successful oncology...
2 years agoOvercoming the Hurdles: Navigating the Challenges in Oncology Clinical Trials
In the world of medical research, oncology clinical trials are at the forefront of innovation and discovery. These trials play a crucial role in advancing our understanding of cancer and developing more effective treatments. However, the path to successful oncology...
2 years ago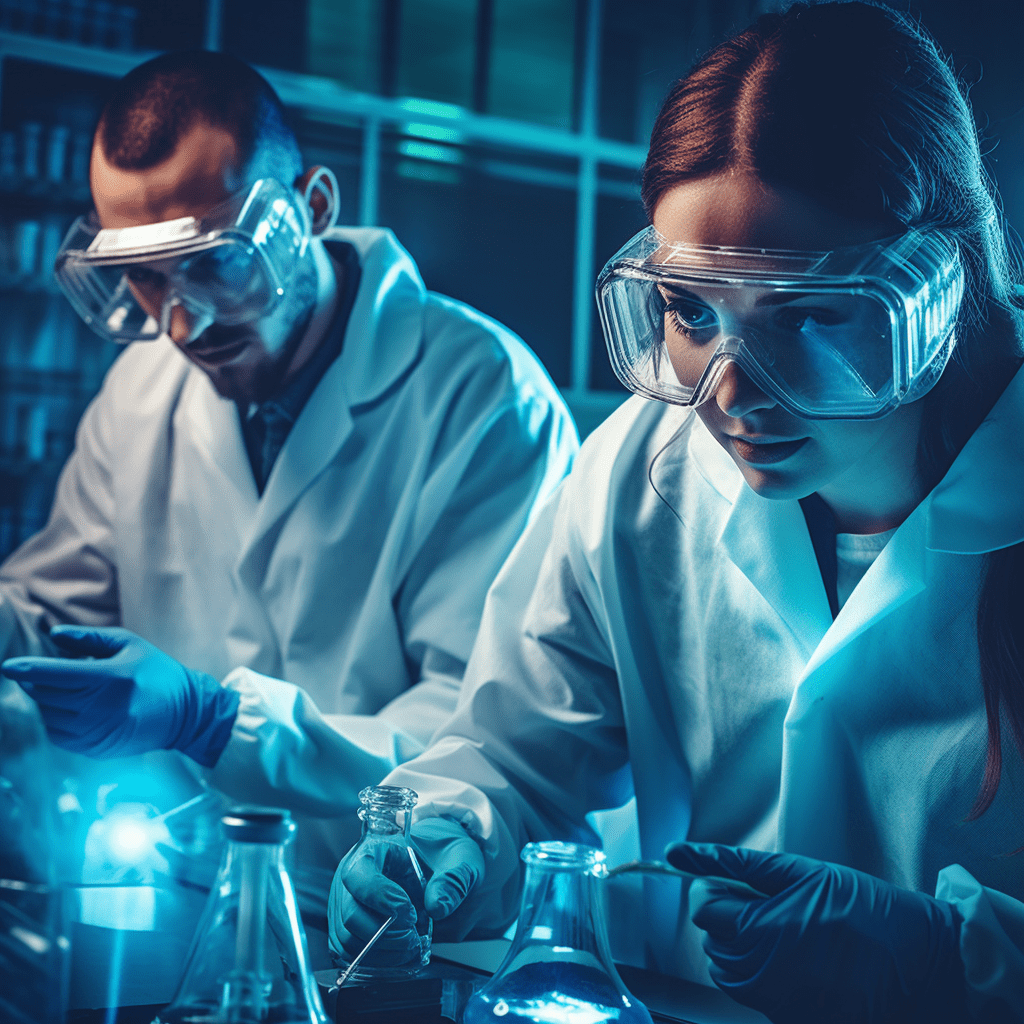
Embracing a Patient-Centric Approach in Oncology Trials
In the realm of healthcare and medical research, the term "patient-centric" has gained significant traction in recent years. This shift in focus towards prioritizing patients' needs and preferences is not only transforming the healthcare industry but is also making waves...
2 years agoEmbracing a Patient-Centric Approach in Oncology Trials
In the realm of healthcare and medical research, the term "patient-centric" has gained significant traction in recent years. This shift in focus towards prioritizing patients' needs and preferences is not only transforming the healthcare industry but is also making waves...
2 years ago